3D XPoint – Three Dimensional cross (X) Point is a form of solid state storage cell arrangement with a vertically layered cell located in a two-dimensional space and with data accessed by a crossover of two wires, aka crosspoint. This was the design used in Intel’s Optane storage-class memory chips.
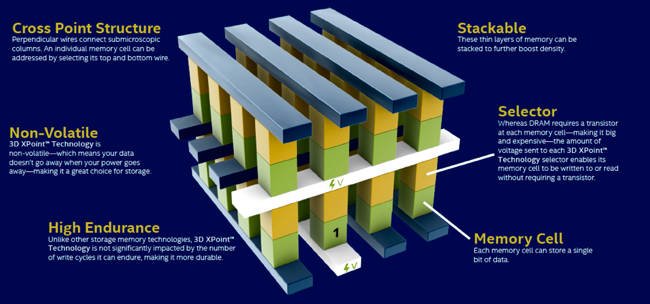