Newly public NAND and SSD maker Kioxia reported sales of ¥450 billion ($3 billion), down 31 percent year-on-year, for its Q3 ended December 31 2024.
These are the first published quarterly numbers since Kioxia’s IPO and Tokyo stock exchange listing in December last year. It also recorded a ¥76.1 billion ($510.7 million) IFRS profit, a turnaround since its year-ago ¥85.9 billion ($594 million) loss. These results were near the middle of Kioxia’s guidance range.
EVP and executive officer Tomoharu Watanabe said: “Overall we continue to see growth in our traditional markets such as smartphones and PCs, and the rapid proliferation of AI, which requires significant amounts of storage, presents an exciting driver for further growth.”
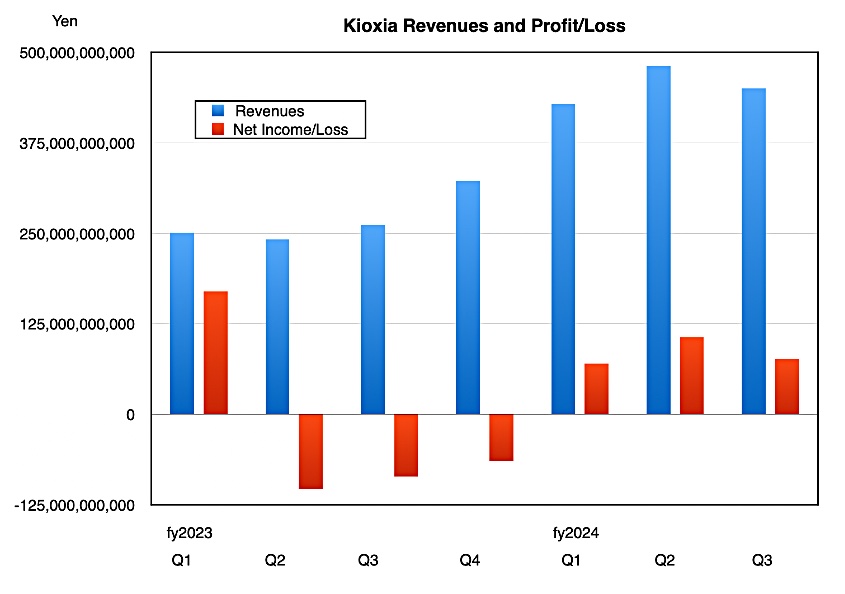
Financial summary
- Free cash flow: ¥77.8 billion ($522 million) compared to prior quarter’s ¥114.9 billion ($751 million).
- Operating cash flow: ¥130.7 billion ($877 million)
- Cash and cash equivalents: ¥174.3 billion ($1.17 billion)
Kioxia splits its revenue sources three ways: SSD and Storage, Smart Devices and Others.
“Others” means retail products such as SD cards and USB sticks plus revenue from chip sales to Western Digital. “Smart Devices” refers to memory for smartphones, tablets, TVs, other consumer devices and the automotive NAND market. “SSD and Storage” refers to NAND and SSD sales to the PC, data center and enterprise markets. A Kioxia chart shows the recent segment revenue history:

There was a 53.5 percent year-over-year rise in Smart Device sales but a sequential 23 percent decline due to phone makers using up inventory rather than buying new NAND.
SSD and Storage revenues have been growing since last year, roughly doubling due to AI server demand and traditional server replacement. Datacenter and enterprise SSD sales accounted for approximately half of this segment’s revenues.
Kioxia’s estimates it market share for datacenter and enterprise SSDs (PICe) in calendar 2023 was about 10 percent. It’s still calculating its calendar 2024 share.
CFO Hideki Hanazawa said customer qualifications of Kioxia’s gen 8 BiCS flash across the three segments were on schedule and he expects a recovery in demand in the second half of calendar 2025.
Kioxia has a joint NAND fabrication partnership with Western Digital and WD’s SSD revenues for its latest quarter were $1.88 billion, up 12 percent year-over-year. Kioxia believes that, with the spin-off of WD’s flash business, SanDisk, “there will be no impact on the business operations or growth of our company and our joint ventures together.”
The outlook is for growth in smartphones, PCs, datacenters and enterprises as well as traditional server SSDs. It will expand BiCS gen 8 production to cater for AI application demand and a general recovery in the NAND sales pipeline in the second half of 2025. Kioxia expects a NAND bit growth rate in the low 10 percent range in calendar 2025 with fourth quarter revenue expected to be ¥330 billion ± ¥15 billion, a 2.5 percent increase on the year-ago Q4 at the mid-point.
Profits in Kioxia’s Q4 will likely be down due to pressure on prices, given the excess inventory currently floating around the industry.
Full FY 2024 revenues should be ¥1.69 trillion ± ¥30 billion ($11.3 billion), a 57 percent year-over-year increase at the midpoint, making it Kioxia’s “highest annual revenue ever.”
Looking ahead, Kioxia says it will focus on SSDs that support PCIe Gen 5. Its BiCS Gen 9 NAND, with 300-plus layers, will be announced later this month.
Bootnote
Unlike US businesses, Japanese company fiscal years are named from the starting calendar year, not the finishing calendar year. Kioxia’s fiscal 2024 year runs from April 2024 to the end of March 2025.