AvePoint has announced the launch of AvePoint Cloud Backup Express, which, running on Microsoft 365 Backup Storage, enables customers to protect and secure their SharePoint, OneDrive, and Exchange environments. It keeps all data within the Microsoft 365 security boundary.
…
Data lakehouse supplier Databricks has integrated technology from generative AI supplier MosaicML – which it bought in June for $1.3 billion – into its own offering to produce a Data Intelligence Platform on top of its lakehouse. It enables customers to create an internal “AI factory” where they can train and deploy models on private data at an accessible cost.
MosaicML now offers multiple capabilities to directly integrate enterprise data into AI systems including:
- End-to-end RAG (Retrieval Augmented Generation) to build high quality conversational agents on your custom data, using Databricks Vector Database for “memory”
- Training custom models either from scratch on an organization’s data or by continued pre-training of existing models such as MPT and Llama 2 to further enhance AI applications with deep understanding of a target domain
- Efficient and secure serverless inference on your enterprise data, and connected into Unity Catalog’s governance and quality monitoring functionality
- End-to-end MLOps based on the popular MLflow open source project, with all produced data automatically actionable, tracked, and monitorable in the lakehouse
Read a blog for more info.
…
Astra DB Database-as-a-Service (DBaaS) supplier DataStax has introduced Astra DB Assistants API, which is a drop-in replacement for the OpenAI Assistants API. OpenAI Assistants API handles all the stateful operations required for large language model-based applications including persistent threads and messages, files, and automatic RAG. Astra says the end result is a simple, scalable datastore for AI apps that’s backed by the power of Cassandra. It is available as a developer preview. Read a blog about it here.
…
DDN has joined the Vultr Cloud Alliance. By integrating DDN’s data management systems with Vultr’s composable cloud infrastructure, data science and engineering teams will gain optimized data operations, migration, and protection for their AI initiatives across Vultr’s global network of 32 cloud datacenter locations. Vultr says it’s the world’s largest privately held cloud computing platform, and offers Cloud GPU (Nvidia), Cloud Compute (VMs), optimized Cloud Compute (NVMe SSDs and VMs), and Bare Metal servers.
…
HPC storage performance watcher Glenn Lockwood writes of DDN’s new Infinia file system software: “The engineering team developing Infinia inside DDN is completely separate from the Whamcloud team who is developing Lustre, but this could be a double-edged sword. On the good side, it means that open-source Lustre development effort isn’t competing with DDN’s proprietary product in engineering priorities on a day-to-day basis. On the bad side though, I still struggle to see how Infinia and Lustre can avoid eventually competing for the same business.
“For the time being, Infinia does seem to prioritize more enterprisey features like multi-tenancy and hands-free operation while Lustre is squarely aimed at delivering maximum performance to a broadening range of workloads. Their paths may eventually cross, but that day is probably a long way off, and Lustre has the benefit of being deeply entrenched across the HPC industry.”
…
Fantom Drives has released its VENOMX SSD for gaming, virtual reality, and video production. There are 1 TB and 2 TB models in the M.2 format, supporting PCIe gen 4 and an NVMe interface. Read/write speeds reach up to 5,100/2,600 MBps. The drive’s feature set includes dynamic caching, TRIM support, SMART (Self-Monitoring, Analysis, and Reporting Technology), APST, LDPC ECC algorithm, end-to-end data path protection, and AES 256-bit encryption. They have up To 1500 TBW endurance and 1.5 million hours of MTBF, and a five-year warranty.

…
Unstructured data orchestrator Hammerspace has hired former AWS GM Mark Cree as SVP of Strategic Partnerships. Cree ran AWS’s storage gateway business. Before that he was CEO and founder of InfiniteIO, which used metadata acceleration to speed file access, not a million miles from what Hammerspace does now.
…
Infinidat said Japanese commercial online karaoke supplier XING consolidated its enterprise storage on the InfiniBox platform five years ago, simplifying its infrastructure (27 storage systems from four different suppliers). As a result, we’re told it improved performance, saved space, and achieved an annual cost saving of 80 percent by substantially reducing the equipment and maintenance costs associated with the previous storage devices, and with no downtime since then. Read a case study here.
…
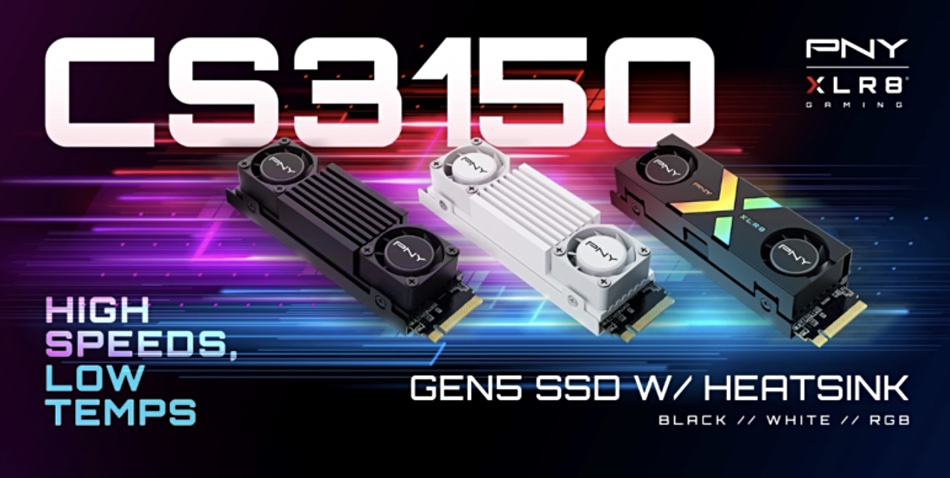
PNY has a CS3150 PCIe gen 5 gaming SSD in M.2 2280 format, operating with up to 12,000 MB/s and 11,000 MB/s sequential read/write speeds, available in 1 TB and 2 TB densities, and comes with dual-fan heatsinks. It uses Microsoft DirectStorage, which was introduced in Windows 11 and improves the speed at which games load and the quality of their images. TCG Opal 2.0 is enabled for hardware encryption and storage security – an odd feature for a gamer’s SSD. The drive has five-year limited warranty and is priced at £165-£175 for 1 TB.
…
Proton has announced its Proton Drive app for macOS which provides encrypted public cloud storage. The app lets you sync files between your Mac and the cloud, access them offline, free up space on your computer, and has end-to-end encryption. Proton says it already supplies Proton Drive apps for iPhone, Android, Windows, and the web. It’s a Dropbox competitor.
…
Real-time analytics platform Rockset has expanded its vector search capabilities with approximate nearest neighbor (ANN), achieving billion-scale similarity search in the cloud. This comes after Rockset raised $44 million in funding in August, and was named a data streaming for AI partner to Confluent.
…

Swissbit has an N3202 high-performance PCIe gen 4 SSD in an M.2 2280 form factor using TLC NAND. It has a DRAM-based controller architecture with endurance of up to 1.5 DWPD over a five-year period. The N3202 is available in 240 GB, 480 GB, 960 GB, and 1920 GB capacities.
…
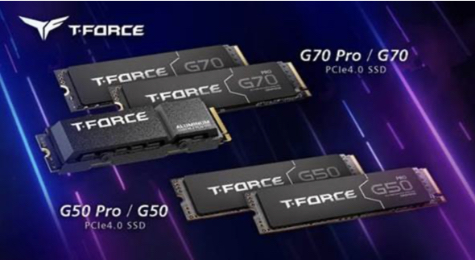
Team Group has released four new T-FORCE PCIe gen 4×4 SSDs: the G70, G70 PRO, G50, and G50 PRO drives, all using InnoGrit’s controller. They are available in the M.2 2280 form factor and come with thin graphene heat sinks. The G70 and G70 PRO SSDs have read speeds of up to 7,000 MBps, while the G50 and G50 PRO SSDs can clock up to 5,000 MBps. The G70 and G50 SSDs support SLC cache technology, and their PRO variants support both DRAM and SLC caching.
…
Thanks to Storage Newsletter, we got to see TrendForce stats for Q3 2023 SSD units and capacity sales by supplier, with both PC SSD and enterprise SAS SSD sales pushing up the numbers. Unit shipments were 93.06 million, 24 percent higher Q/Q, with client SSD units rising 27 percent and enterprise PCIe SSD units going up 34 percent to 3.77 million ships. The increased client ships helped overall NAND bits to rise 6 percent to 205.35 EB. SAS SSD units grew 26 percent Q/Q, reaching 0.702 million, while enterprise SATA SSDs dropped 5 percent to 3.34 million, with SAS SSDs squeezed between NVMe and SATA. The supplier units and capacity shipped shares were:
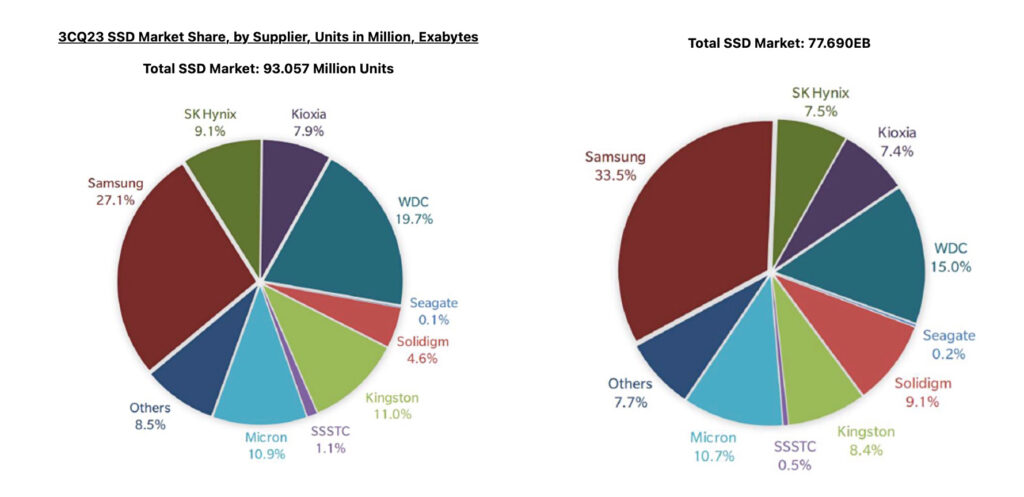
In unit terms Samsung is the clear leader, with Western Digital in second place followed by Kingston, which is not a NAND manufacturer, and then Micron, which is in fourth place. If SK hynix and its subsidiary Solidigm’s shares are combined, they would have 13.7 percent, putting them in third place. Were we to combine Kioxia and NAND foundry joint venture partner Western Digital’s shares, we get 27.6 percent, putting the pair ahead of Samsung in unit shipments.
Doing the same calculation with capacity shipment shares puts the duo at 22.4 percent, well behind Samsung’s leading 33.5 percent share. Combining SK hynix and Solidigm capacities produces a 16.6 percent share, putting them in second place ahead of Western Digital on its own at 15 percent.
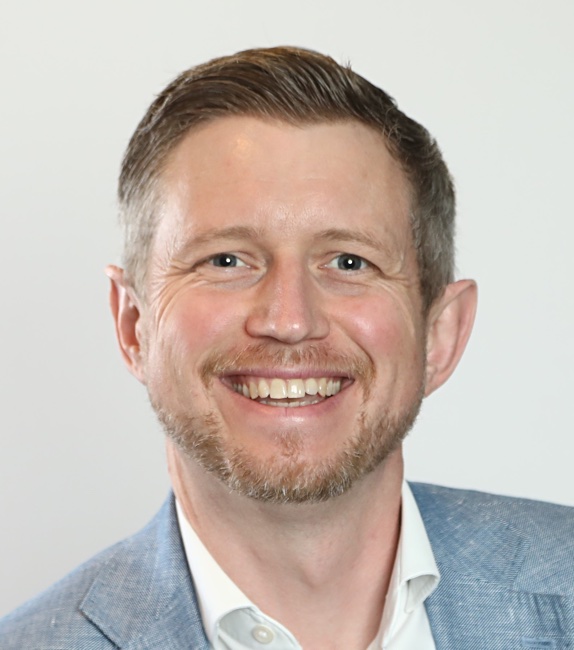
…
Data protector/manager Veritas has hired Richard Wainwright as field CTO for UK and Ireland to lead a team of technical specialists and be responsible for technology strategy and solution architecture. Wainwright joins Veritas from fintech startup R3, where he led the development of a SaaS platform for Corda, a distributed ledger technology. His CV includes stints at Tectrade, Dimension Data, Nortel, and Avaya. Veritas also released market research that shows that nearly half of all global organizations may be miscalculating the severity of threats to their business.
…
ReRAM startup Weebit Nano says it has received the first wafers integrating its embedded ReRAM manufactured in GlobalFoundries’ 22FDX platform. Initial tests of the wafers in this advanced 22 nm FD-SOI (fully depleted silicon on insulator) are showing positive results on the array. Weebit says 22 nm is a geometry where embedded flash is not viable.
…
Weebit and SkyWater announced that Weebit’s ReRAM IP module has been fully qualified in SkyWater’s S130 process at temperatures of up to 125°C – the temperature specified for Grade-1 automotive applications.