GCRAM – Gain-Cell Random Access Memory. The requires 3 transistors to store a bit of data, as opposed to the 6-8 transistors needed for SRAM-based highest-density memory technology. When used with System-on-Chips (SoCs) GCRAM can provide 50% area reduction over high-density SRAM and reduce power consumption by a factor of five. GCRAM can be manufactured using the standard CMOS process. Startup RAAAM Technologies says GCRAM technology combines the density advantages of embedded DRAM with SRAM performance, without any modifications to the standard CMOS process.
RAAAM Memory Technologies’ GCRAM uses separate read and write ports, in contrast to DRAM’s combined read/write port per cell. This enables it to amplify the cell’s stored charge and separately optimize the read and write processes while retaining SRAM-like performance.
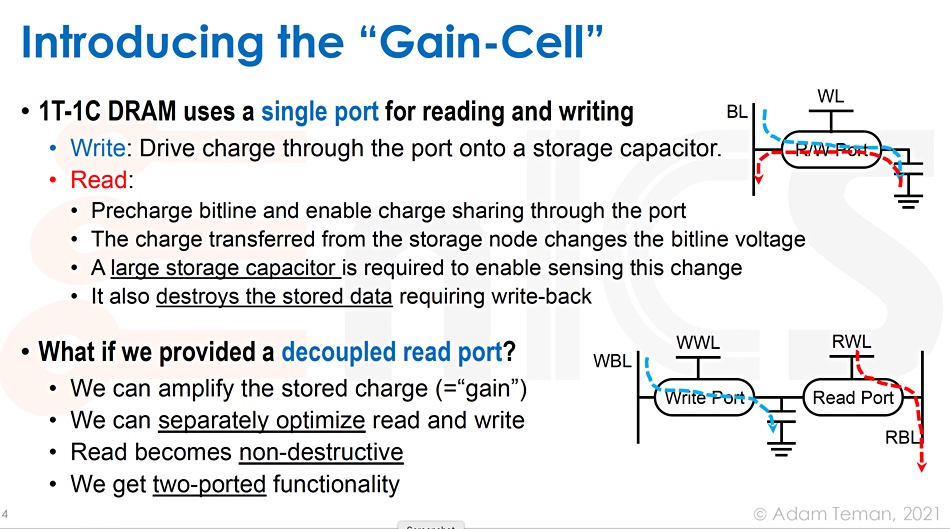