Host Bus Adapter – A block interface device to connect a server’s PCI bus to a Fibre Channel, SCSI or SATA network linking it to a block storage device. HBAs, in other words, are used to connect servers to SANs. They exist at the server and SAN end of the network link and, in the Fibre Channel situation, support a specific generation of Fibre Channel. They are generally backwards-compatible with prior generations.
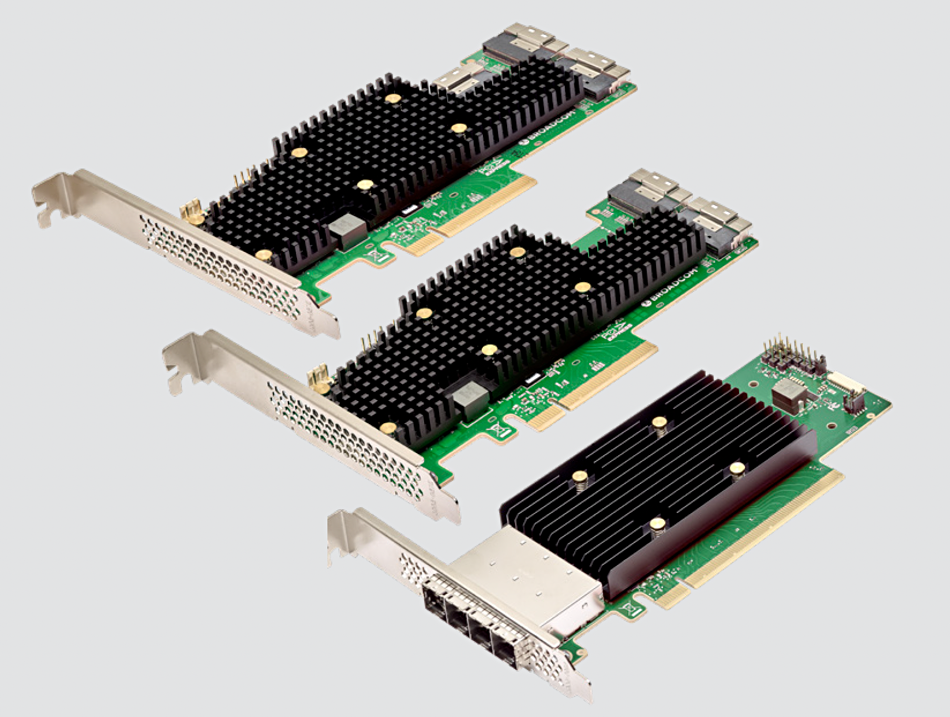
HBAs can link direct to a destination HBA or to intervening switches or directors (major switches) which aggregate FC links.