Tape – A long ribbon with a magnetic surface which can be used for storing data in parallel tracks running the length of the tape. Data on the tape is not randomly accessed as the tape has to be streamed through a drive to the right location for the data. Because of this tape has a slower data access speed than both SSD (fastest) and disk (intermediate speed). Tape is used for storing backup data and archival data where the access speed is less important than capacity and cost.
Tape is contained in cartridges and these can be stored offline and consume no energy, making archival tape storage low cost. They also last for up to 30 years if stored at the appropriate temperature and humidity, also suiting archival storage needs. Offline tape cannot have its contents deleted or altered by a cyber-attack as there is a physical air gap between the tape cartridge and any accessing IT system.
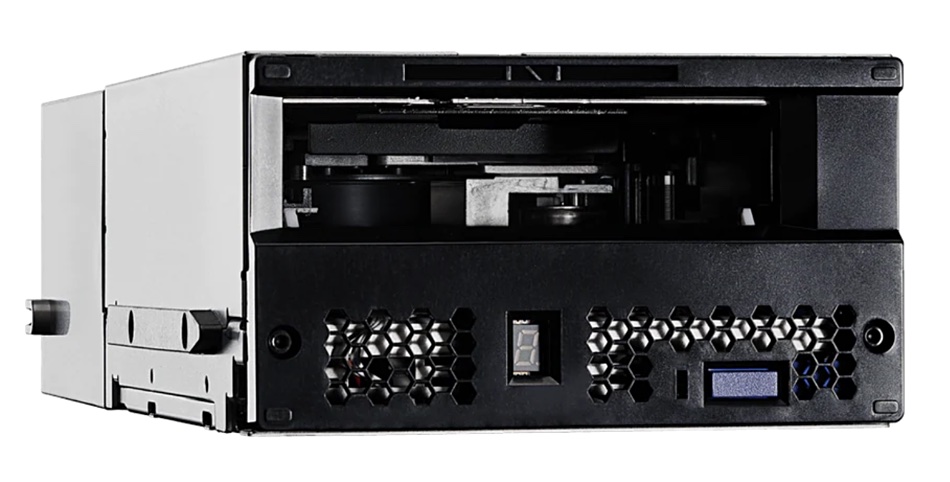
Tape cartridges are loaded into drives, which stream the tape past a read-write head to read and write data. The drives can be part of an autoloader device which stores a few tapes and can feed them to the drive or drives as required. Very large tape libraries store hundreds or thousands of tape cartridges and have robot mechanisms to move them to and from storage shelves to the several drives in the library.
Tape cartridges can also be stored in offline vaults by companies such as Iron Mountain if a reference copy of data is needed for a very long time and has low access needs.
The most popular tape format is LTO with Oracle and IBM making alternative proprietary tape formats. A raft of other formats, such as Quantum’s DLT, have died due to LTO replacing them.