The top two public clouds – Amazon’s and Microsoft’s – lead the distributed HCI market in Gartner’s Magic Quadrant (MQ) report, with Nutanix and Broadcom (VMware) following close behind.
Gartner stopped doing MQ reports on the hyperconverged infrastructure (HCI) appliance market last year and transitioned to looking at the distributed HCI suppliers (DHI), providing edge and datacenter/colo on-premises systems as well as public cloud HCI offerings.
The research house defines distributed hybrid infrastructure as “offerings that deliver cloud-native attributes, which can be deployed and operated where the customer prefers.” It contrasts this with public cloud IaaS, “which is based on a centralized approach.”
Its strategic planning assumption is that: “By 2026, 50 percent of enterprises will initiate proofs of concept for alternative distributed hybrid infrastructure (DHI) products to replace their VMware-based deployments and embrace hybrid cloud infrastructure delivery, up from 10 percent in 2024.” That’s good news for Nutanix and Oracle in North America and elsewhere, and the Chinese distributed HCI suppliers who are subject to geopolitical US-China tensions and effectively locked out of American-influenced markets.
Gartner’s first distributed HCI MQ lists nine suppliers, with Microsoft Azure, AWS, Nutanix, Broadcom, and Oracle classed as Leaders:
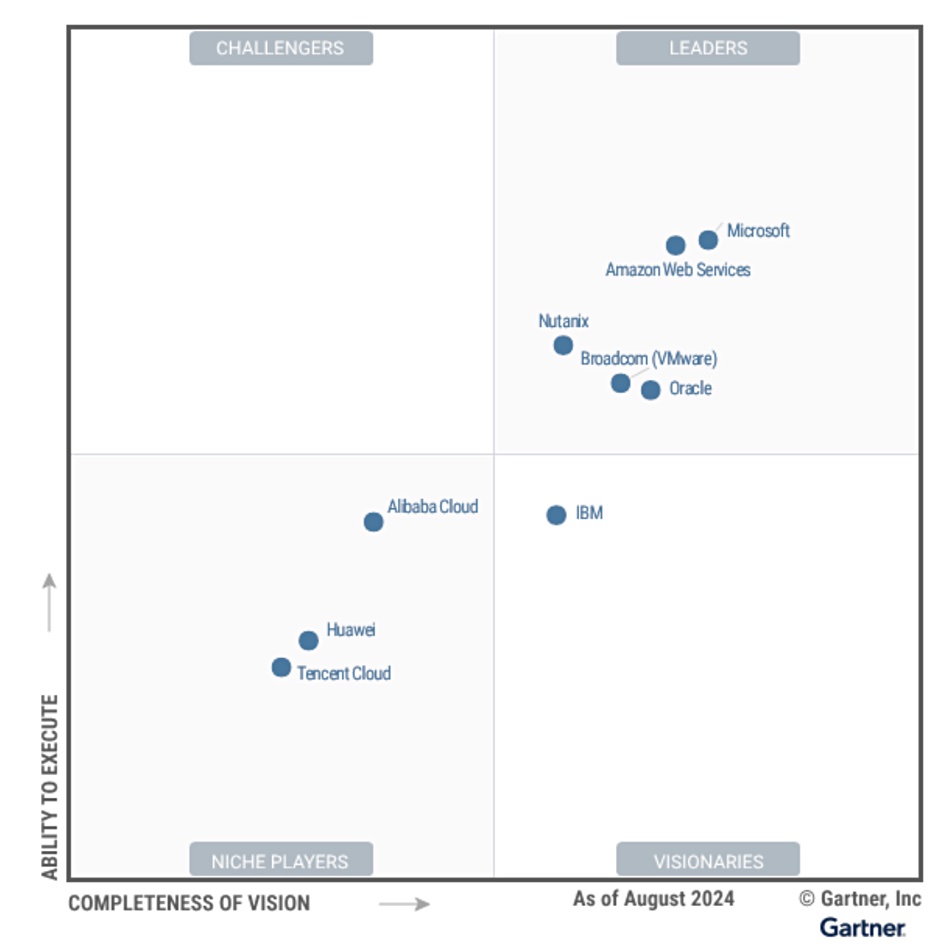
There are no Challengers and three Niche Players, all Chinese suppliers: Alibaba Cloud, Huawei, and Tencent Cloud. IBM is the sole “visionary.”
Appliance-based HCI systems from Dell (VxRail and PowerFlex), HPE (Alletra 5000 and SimpliVity), Quantum (Pivot3), and Scale Computing (HyperCore) are not mentioned in this MQ. The basic inclusion criterion for them is a full public cloud port followed by other entry qualifications:
- Must show evidence of 60 enterprise customers deploying products in distributed hybrid infrastructure scenarios or must have reported over $50 million in ARR contract value as of 1 May 2024.
- Must show evidence that all DHI production customer deployments are across on-premises and at least one hyperscale strategic public cloud environment (see Magic Quadrant for Strategic Cloud Platform Services). For hyperscale cloud providers, there should be evidence of on-premises or edge DHI deployment and software providers or full-stack HCI vendors, as well as evidence of the deployment of a DHI offering in the hyperscale strategic public cloud.
Gartner gives honorable mentions to Google (Google Distributed Cloud), Red Hat (OpenShift), and SUSE (Harvester).
William Blair financial analyst Jason Ader discusses Nutanix, telling subscribers: “A lot of things are falling into place for the company—from the large VMware displacement opportunity to the addition of new OEM partners, the buildout of a modern container platform, and an improving financial model. … The disruption caused by Broadcom’s acquisition of VMware has created a huge vacuum in the infrastructure software space that Nutanix believes it can fill.”
There is opportunity here for the other DHI players mentioned by Gartner, and also the HCI appliance vendors.