Aerospike unveiled Database 8, a major upgrade of its flagship multi-model distributed database. V8 adds distributed ACID transactions to support large-scale online transaction processing (OLTP) applications. Aerospike says v 8 is the first real-time distributed database to guarantee strict serializability of ACID transactions with efficiency, claiming it’s a fraction of the cost of other systems.
…
Data mover Airbyte is offering customers predictable pricing based on capacity – rather than data volumes – to accommodate their need for artificial intelligence (AI), data lakes, and real-time analytics. A pilot rollout with customers over the past few months has met with overwhelmingly positive responses, plus the company gathered feedback from more than 500 organizations that cited issues with unpredictability and cost spikes with traditional volume pricing models. The new pricing applies to Airbyte Teams and Enterprise products with pricing determined by the number of connections/data sources, frequency of data refreshes (daily, hourly, real-time), and the pipeline scheduling requirements.
For Airbyte Cloud, there are no changes because pay-as-you-go and credit-based pricing can work well for specific customers, especially smaller organizations with fewer data sources and more predictable data needs that benefit from not having to build and maintain that infrastructure themselves. More details here.
…
Ataccama, an enterprise data quality, data management, and data governance player, has launched Ataccama Lineage, a new module within Ataccama ONE, its flagship Ataccama unified data trust platform. It says Lineage provides enterprise-wide visibility into data flows, offering organizations a view of their data’s journey from source to consumption. It helps teams trace data origins, resolve issue, and ensure compliance. It’s integrated with Ataccama’s data quality, observability, governance, and master data management capabilities, and enables organizations to make faster, more informed decisions, such as ensuring audit readiness and meeting regulatory compliance requirements.
…
Cobalt Iron says its Compass enterprise SaaS backup platform has been recognized as a TOP 5 Enterprise VMware Backup Solution for 2025-26 by DCIG. Download the 2025-26 DCIG TOP 5 Enterprise VMWare Backup report here
…
Commvault announced that the Commvault Cloud Platform can be deployed from the AWS, Azure, GCP and VMware marketplaces utilizing CIS-hardened images. These are SW files that are pre-configured to align with the Center for Internet Security (CIS) Benchmarks to meet security benchmarks out-of-the-box.
…
Data streamer Confluent and data lakehouser Databricks have a partnership and added new bi-directional integrations between Confluent’s Tableflow, Deltalake and Databricks Unity Catalog to provide customers with real-time data for AI-driven decision-making. Tableflow with Delta Lake makes operational data available immediately to Delta Lake’s ecosystem. Confluent and Databricks customers will be able to bring any engine or AI tool such as Apache Spark, Trino, Polars, DuckDB and Daft to their data in Unity Catalog. Tableflow with Delta Lake makes operational data available immediately to Delta Lake’s ecosystem. Confluent and Databricks customers will be able to bring any engine or AI tool such as Apache Spark, Trino, Polars, DuckDB and Daft to their data in Unity Catalog. Operational data from Confluent becomes a first-class citizen in Databricks, and Databricks data is accessible by any processor in the enterprise.
…
Databricks has launched SAP Databricks, a strategic product and go-to-market partnership with SAP that natively integrates the Databricks Data Intelligence Platform within the newly launched SAP Business Data Cloud. The partnership combines business data in SAP with the Databricks platform for data warehousing, data engineering, and AI all governed by Databricks Unity Catalog. SAP Databricks allows customers to combine their SAP data with the rest of their enterprise data. Through bi-directional sharing of data via Delta Sharing between their SAP Databricks environment and their native Databricks (non-SAP) environment, they can unify all their data without complicated data engineering.
SAP Databricks is sold by SAP as part of SAP Business Data Cloud, and will be available in a staged rollout on AWS, Azure and Google Cloud.
…
As part of its big Infinia object storage for AI launch, and following its $300 million Blackstone investment, DDN is hiring execs. Moiz Kohari is DDN’s VP of Enterprise AI and Augmented insights. Doug Cook is VP of Global System Integrators. Santosh Erram is VP of Strategic Partnerships and Business Development, working with NVIDIA, hyperscalers and AI.
…
Accelerated Compute Fabric (ACF) switch chip developer Enfabrica the opening of Enfabrica India, a Hyderabad-based office and R&D center to grow the company’s global footprint, attract the engineering and development talent, and scale its silicon and software product development operations. The AI market in India is projected to reach $8 billion by 2025, growing at a compound annual growth rate of over 40 percent rom 2020 to 2025. Enfabrica is building its team amongst Hyderabad’s vibrant academic community of talented engineers and developers.
…

AI-focused data warehouser Firebolt has hired Hemanth Vedagarbha has its first-ever president. He will oversee all go-to-market (GTM) and customer-facing functions – including Sales, Customer Success, Marketing, Business Development, Field Engineering, Technical Support, Revenue Operations and Partnerships & Ecosystems. He brings over 20 years of “successful, high-growth enterprise SaaS experience at industry-leading companies such as Oracle and most recently Confluent.”
…
Data mover Fivetran has appointed Simon Quinton as GM for EMEA, Suresh Seshadri as CFO and Anand Mehta as Chief People Officer (CPO).
…
Forrester has issued a Forrester Wave: Translytical Data Platforms, Q4 2024 report, with Oracle at the top of the translytical tree, followed by MongoDB, Google and InterSystems. SingleStore is the leading strong performer. Get a copy of the report here.
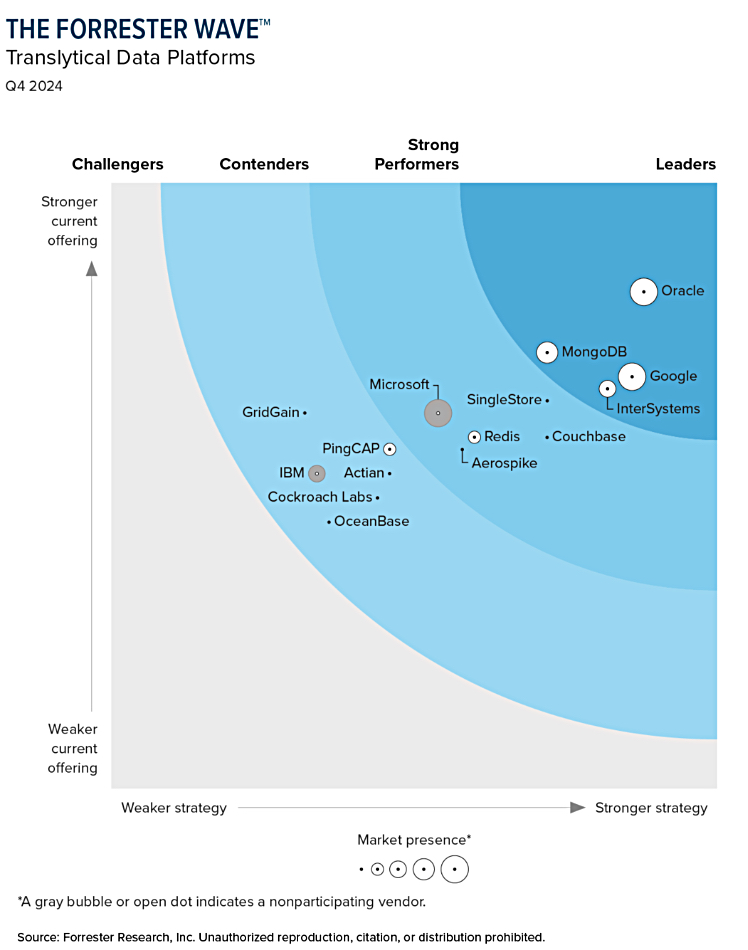
…
HarperDB says it collapses fragmented systems like MongoDB, Redis, Kafka and application servers into one, high-performant technology platform, removing layers of resource-consuming logic, serialization, and network processes between each technology in the stack (data, application, cache, and messaging). HarperDB users get a low-latency system with “limitless” horizontal scale. They could achieve 7x faster page loads and nearly 30x faster LCPs (time to largest contentful point), the company claims. Common backend processes take 100+ milliseconds on traditional systems, but take only .2-1 millisecond with HarperDB, it claims.
…
Hitachi Vantara is allying with BMC Software to combine its VSP One and Hitachi Content Platform (HCP) offerings storage platform’s with BMC’s AMI mainframe SW to help mainframe users reduce costs, optimize operations and secure mainframe data. The AMI products involved are AMI Cloud, AMI Security, AMI Ops and AMI devX.
…
Log data streaming data lake supplier Hydrolix has achieved the Amazon CloudFront Ready designation, part of the Amazon Web Services (AWS) Service Ready Program. Hydrolix integrates with AWS CloudFront, WAF and Elemental services. More edge services integrations are coming in the first half of 2025.
…
Hydrolix announced a new connector for Apache Spark to enable Databricks users to store massive amounts of time series data over long periods of time at full fidelity in the Hydrolix data lake. Using Hydrolix, Databricks users can now unleash the analytical power of Databricks against all of their data and model across longer time periods, such as year-over-year and multiyear data sets, to gain better insights.
…
Lenovo research finds that, In 2025, AI budgets are expected to nearly triple compared to the previous year, comprising nearly 20 percent of total IT budgets. 63 percent of organizations globally prefer using on-premises and/or hybrid infrastructure/ deployments for AI workloads. Data science, along with IT services and infrastructure, will be the top AI areas of investment over the next 12 months. 42 percent of organizations are expected to focus on implementing GenAI use cases, a significant increase from 11 percent in 2024. Fill out a form to download an eBook about this here.
…
Multi-cloud storage manager startup Lucidity announced a $21 million Series A investment led by WestBridge Capital with participation from existing investor Alpha Wave. Its cloud management SW automates block storage expansion and shrinking of storage volumes based on real-time data demands, helping the world’s largest enterprises cut costs by up to 70 percent. Its NoOps, autonomous, application-agnostic layer seamlessly integrates with existing applications and environments – without requiring any code to be changed. Since its founding in 2021, Lucidity says it has achieved 400 percent year-over-year growth, although as a private outfit, it does not provide base figures.
Nitin Bhadauria, Cofounder at Lucidity said. “Lucidity delivers the only platform for ITOps and DevOps organisations to automatically manage and optimize their block storage in real-time across all three major cloud providers while significantly reducing costs.”
…
Open-source, in-memory graph database supplier Memgraph has v3.0 SW which it says will enable firms to make their data GenAI-ready and create applications, such as chatbots or agents, that are more-performant. It integrates vector search to combine the creative power of LLMs with the precision of knowledge graphs. GenAI applications powered by 3.0’s standout feature, Retrieval-Augmented Generation in graph (or GraphRAG), enhance reasoning, reduce hallucinations, and work securely within an enterprise’s unique context and data. It has unique dynamic algorithms, tailored for real-time data analysis and high-throughput use cases which enable fast, continuous responses to incoming data without requiring LLM retraining. Users can quickly create knowledge graphs that enhance LLMs, while preventing the accidental exposure of proprietary information, safeguarding an organization’s IP.
…
Cloud file services supplier Nasuni says in 2024 it grew its revenue by 26 percent and stayed profitable and cash flow positive. It now manages over 500 petabytes of total capacity. More than half of its customer base also expanded their deployments, with over 600 expansions recorded throughout the year. Nasuni customers include Mattel, Autodesk, Tetra Tech, Dow, Dyson, Boston Scientific, and the State of Arizona. It increased its global workforce to just under 600, with many employees based out of its Boston headquarters and in the United Kingdom, Ireland, India, and other locations.
…
Nutanix released findings for its 7th annual Enterprise Cloud Index, saying 80 percent of organizations have already implemented a GenAI strategy. It added that 98 percent of respondents face challenges when it comes to scaling GenAI workloads from development to production. The #1 challenge associated with this is integration with existing IT infrastructure. Have a look at the report here.
…
Back in October 2024 Overland Tandberg said it was exiting the tape archive data protection business to focus on its RDX removable disk drive offerings. Tape storage hardware and services supplier MagStor has just announced availability of Transition and Support Services specifically for Overland Tandberg customers and resellers. MagStor sells tape hardware that is compatible with Overland Tandberg tape hardware products. Overland customers and resellers can contact MagStor for pricing on solutions to replace their Overland branded products. MagStor MSRP pricing is always lower than the former Overland Tandberg products as well. More information here.
…
OWC (Other World Computing), which supplies high-performance storage, docks, and memory cards for video and audio production, photography, and business, and ARCHIWARE, a provider of data management SW, have a strategic partnership to deliver shared storage, cloning, backup, and archiving for collaborative workflows. The ARCHIWARE P5 platform will now be natively integrated with the OWC’s Jellyfish Shared Storage for Video Production to enhance collaboration capabilities, ensure data protection, and future-proof asset management.)
…
OWC announced GA of Dock Ejector 2.0, for efficiently and safely ejecting all connected devices, including SoftRAID and AppleRAID volumes. This updated version works with all docks, including non-OWC docks and hubs, expanding compatibility and drive protection to all Mac and PC users. By ensuring all data has been written before any disk is unmounted, you can safely eject your dock without worrying about losing or fragmenting files.
…
PNY Technologies announced a new office in Saudi Arabia to strengthen PNY’s local presence to support businesses in their AI and digital transformation projects.
…
Snowflake unveiled Cortex Agents, a fully managed service that simplifies integration, retrieval and processing of structured and unstructured data to enable Snowflake customers to build high-quality AI agents at scale. Cortex Agents, now available in public preview, orchestrates across structured and unstructured data sources, whether it be Snowflake tables or PDF files stored in object storage, and breaks down complex queries, retrieves relevant data and generates precise answers, using Cortex Search, Cortex Analyst and LLMs. Cortex Analyst is now generally available with Anthropic Claude as a key LLM powering agentic text-to-SQL for high-quality structured data retrieval. Cortex Search has achieved state-of-the-art quality unstructured data retrieval accuracy, beating OpenAI embedding models by at least 12 percent across a diverse set of benchmarks including (NDCG@10).
…
Virtualized datacenter supplier VergeIO had a great final 2024 quarter, booking 100 percent more new annual contract value (ACV) than the prior quarter and 12 percent more than VergeIO’s previous record set in Q1 2024. New customers won nearly doubled, setting a new record. A global hyperscaler is funding a POC showing how VergeOS can virtualize NVIDIA’s latest GPU to be used remotely on another host for AI workloads. It anticipates winning additional new enterprise accounts with the launch of VergeOS on a global data center provider’s bare-metal offerings.