Western Digital and Sandisk started trading their stocks as separate businesses on February 24, with Western Digital shares losing 2.9 percent and Sandisk’s 7 percent of their value, which, in stock market value terms, justifies their separation.
The day before they started trading separately, Western Digital shares were priced at $51.90 with a market capitalization of $17.94 billion based on 345.71 million outstanding shares. The next day, they opened at $52.61 and finished at $49.02, with a $16.95 billion market capitalization. SanDisk started its separate trading on February 24 at $52.20, finishing the day at $48.60. Given its 115.24 million shares and 0.33333 share ratio against Western Digital’s shares, this results in a market cap of $5.6 billion.
Thus, the day before the split, Western Digital – including its Sandisk operation – was valued at $17.94 billion. The day after the split, Western Digital was valued at $16.95 billion and Sandisk at $5.6 billion, a combined total of $22.55 billion. This gives justification to activist investor Elliott Management, which pushed for separation.
Back in May 2022, Elliott revealed that it had a stake in Western Digital and published a letter calling for Sandisk to be spun out as the overall shareholder value of Western Digital and Sandisk could be much greater if its HDD and SSD businesses were separated. Nearly three years later, the split has taken place, and Elliott Management’s view has been vindicated.
Sandisk published some financial history at a February 12 investor day, providing revenue, GAAP net income, and free cash flow numbers:
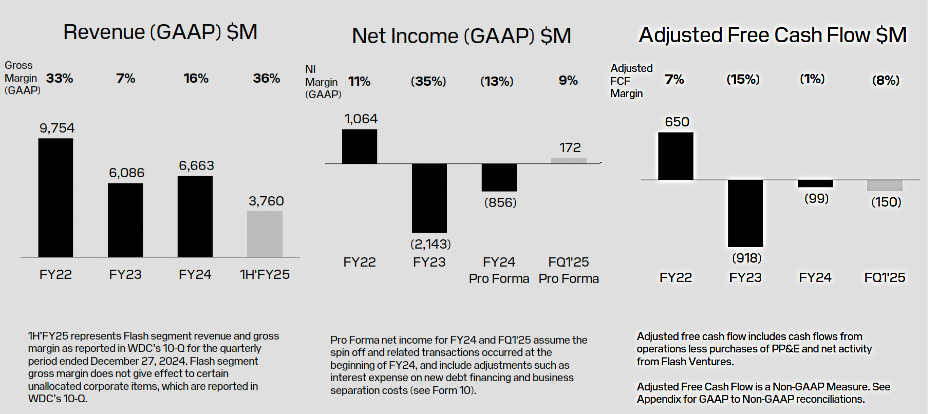
They show a decline in revenue from FY 2022’s $9.75 billion to FY 2024’s $6.66 billion, along with losses and negative free cash flow in FY 2023 and FY 2024. CEO David Goeckeler said Sandisk should generate positive free cash flow at a $10 billion/year revenue level. It may generate revenue of $7.5 billion in FY 2025 and reach $10 billion in three years at a 10 percent annual growth rate.
Sandisk’s joint venture partner, Kioxia, projects full-year 2024-2025 revenue of $11.3 billion, considerably more than Sandisk is likely to earn. If each company receives half of the NAND chip output from their joint-venture fabs, then Kioxia is doing a better job of monetizing NAND chips. Will Elliott Management now sell its Sandisk shares? Or will it examine the apparent disparity between Kioxia and Sandisk’s earnings from their shared JV and consider how to capitalize on it?